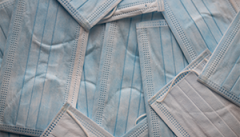
Research
Protective masks and recycling: compatible?
Today on our noses and tomorrow in nature.
Summer 2070, on the beach. Stranded on the sand: the protective mask we once wore after lockdown to go shopping or to the office. Like an old forgotten friend on whom we had relied, it has not changed. Perhaps slightly blackened by the polluted air, it displays fibres that are still intact.
With a very short lifespan, disposable protective masks are a considerable source of waste. Incorrectly disposed of or even sometimes abandoned in the street like a cigarette butt, the masks that protect us today could harm us tomorrow. Is it possible to recycle them? Do we need to consider designing biodegradable masks? Jean-François Gérard, researcher at the Polymer Materials Engineering Laboratory (IMP) and professor in the Materials Science and Engineering Department, takes stock of the situation. Interview.
It is now part of our daily routine as soon as we leave home: to make sure we have a mask. What is this travel companion made of?
Surgical masks are made of polypropylene. This polymer is one of the most produced on earth because it is cheap and easy to obtain. Moreover, it makes up most of the items that surround us, such as food packaging and parts for household appliances. Surgical masks are manufactured by a melt-blowing process, from polypropylene melted by spinning at very high pressure and in an intense air flow. Polypropylene stretches to form fibres of a few microns. The polypropylene used in this process has a very low viscosity, similar to that of water, making it possible to provide this light non-woven material of about fifteen grammes per m². It is tear-resistant, porous to allow air to pass through and tight enough to hold the famous droplets. Generally, the disposable masks we wear are made up of two or three superimposed layers of this non-woven material, formed by fibres that cross over each other, allowing the functions of filtration and breathability. Another distinctive feature of polypropylene is its ability to charge itself with static electricity on the surface. It is perhaps less well known, but it is a very useful phenomenon, because electrostatic attraction contributes to the filtration of particles. This is also one of the reasons why protective masks have a limited lifespan: the more time passes, the more the electrostatic charge decreases, reducing the effectiveness of the mask!
With a duration of effectiveness of 4 hours, the mask quickly becomes invasive waste. Could the masks be recycled or reused?
In theory, it is quite possible to fully recycle polypropylene. If it is well sorted, it is easy to recycle. In the end, a mask is very little material, about five grammes, and the very specific polypropylene used has a very low mechanical resistance, which would require it to be re-mixed with polypropylenes from other waste or virgin materials. Another way of theoretically combating the rapid obsolescence of surgical masks, and their accumulation as waste in large quantities, would be to reuse them. Many processes have been studied to clean up these objects by immersing them in hypercritical fluids such as CO2, ethylene oxide, or under hydrogen pressure to eliminate viruses and bacteria. At the Polymer Materials Engineering Laboratory1, we have proposed the use of microwaves to clean the masks. However, the main problem lies well upstream, whatever the recycling and re-processing route: the conditions for collecting from the various sources of consumption, particularly individuals, are not sufficiently safe, as the aim here is to treat waste that is potentially contaminated and therefore dangerous for those collecting them. Moreover, in hospitals, masks are collected and disposed of by incineration to avoid any risk of further contamination.
To limit the production of waste linked to the consumption of masks, could we imagine the use of biodegradable masks?
If there is any certainty, it is that disposable polypropylene masks do not biodegrade. In order for a material to decompose in a biological medium, certain conditions for degradation, i.e. reaction by micro-organisms in the medium, must be met. Here, the polymer is too stable for enzymes to be able to break it down by fragmenting it until it is eliminated. Its only enemy would be ultraviolet rays. Making biodegradable masks would be a false good idea since, apart from the fact that it is hazardous waste, we are not equipped in France with sites capable of doing biodegradability on a large scale, knowing that what is biodegradable is not necessarily good for the environment! Furthermore, there is a risk that stamping a mask as 'biodegradable’ may lead some consumers to throw them away anywhere... To avoid the invasion of this waste, only the wearing of a mask made of reusable fabric can counter the massive production of mask waste.
Could we then imagine a recycling sector specialising in single-use masks?
Personally, I don't think this is a good idea for reasons of economic reality. Today, the waste recycling industry is very concerned about the recyclability of its plastic products in the face of the safety rules imposed by the health crisis, and recycling protective masks could endanger the health of sorting operators. Even if polypropylene masks are theoretically easy to recycle, it is not necessarily easy to find a second life for them in the form of a new mask or object. And how many times could a mask be recycled? It would need to be stamped each time it is recycled, not to mention that it will lose some of its filtering power each time it is reused. There also remains the question of social acceptability: who will agree to wear a re-treated mask? I believe that the best thing to do today is to carefully throw your mask in the bin, making sure you close the bag carefully because the object that has protected us for a few hours could contaminate those collecting it who remove our waste every day.
1 The laboratoire IMP is a joint research unit of the CNRS (UMR CNRS 5223), located on three University of Lyon sites: INSA Lyon, Claude Bernard Lyon 1 University and Jean Monnet de St Etienne University.