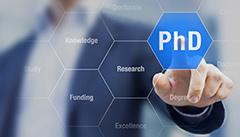
Sciences & Société
Soutenance de thèse : Samuel SIMAGA
Impression 3D de Batteries Lithium-ion par Direct lnk Writing
Doctorant : Samuel SIMAGA
Laboratoire INSA : MATEIS - Matériaux Ingénierie et Sciences
École doctorale : ED34 Matériaux
La demande croissante en sources d'énergie électrique autonomes pousse à repenser les méthodes de stockage de l'énergie. Parmi les différentes technologies disponibles, le stockage électrochimique en batterie lithium-ion se distingue par sa densité énergétique élevée. Toutefois, la conception des cellules Li-ion et le processus d'enduction des électrodes n'ont pas fait l'objet de changements significatifs depuis l'émergence des premières batteries commerciales de ce type. Dans ce contexte, la fabrication additive apparaît comme une approche prometteuse permettant l'accès à des assemblages au design complexe, inaccessibles avec les méthodes de fabrication traditionnelles. Les travaux présentés dans ce manuscrit couvrent le développement de formulations d'électrodes à faible empreinte environnementale, compatibles avec la technique de fabrication additive Direct lnk Writing (DIW). Cette technique permet d'imprimer des matériaux couche par couche en 3D avec, dans le cas présent, une résolution de 200 micromètres. Des formulations d'encres aqueuses d'électrodes de batterie lithium-ion à base de graphite et de LiFePO. ont été développées, dans ce travail. Les propriétés rhéologiques des encres ont été optimisées pour permettre une impression par DIW avec des taux de matière active élevés (près de 90 %) tout en présentant après séchages des propriétés électriques et mécaniques appropriées pour leur utilisation en tant qu'électrodes. Ces électrodes imprimées affichent des performances électrochimiques remarquables en offrant une capacité similaire à celle des électrodes enduites de manière traditionnelle. Ces électrodes imprimables amènent à un changement de paradigme concernant la cellule, notamment la prise de contact électriques et l'encapsulation. Ces travaux ont également permis de proposer des pistes de recherche et de présenter des premiers résultats concernant des cellules conçues pour des structures complexes, telles que des motifs cathodes/anodes interdigités. En conclusion, l'impression 3D par DIW apparaît comme une méthode prometteuse pour la conception de microbatteries lithium-ion, offrant une voie attractive
pour répondre à la demande croissante de dispositifs portables ou de batteries lithium-ion architecturées. L'impact environnemental a été considéré dans ces travaux en sélectionnant des matériaux dont la mise en œuvre peut être réalisée dans l'eau et qui sont abondants.
Additional informations
-
Amphithéâtre Marc Seguin, Amphithéâtre Marc Seguin INSA Lyon, 27 Av. Jean Capelle 0, 69100 Villeurbanne
Keywords (tags)
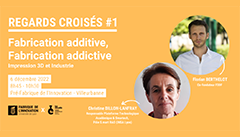
Sciences & Société
"Fabrication additive, fabrication addictive" - Impression 3D et industrie
La fabrication additive, on ne peut plus s'en passer ! Auparavant cantonnée à l'univers de la recherche et à des fonctions de prototypage, la fabrication additive (ou impression 3D) est devenue un véritable outil de formation et un incontournable de la transformation digitale des entreprises.
Désormais enseignée, entre autres, dans les salles de TP des étudiants ingénieurs, elle fait partie intégrante du secteur industriel qui l'utilise à la fois comme outil pour stimuler l’innovation, mais aussi optimiser la supply chain, concevoir de l'outillage, améliorer l’ergonomie des postes de travail, passer d'une logique de prototypage à une démarche produit...
Comment le secteur industriel s'est emparé de la fabrication additive et pour quels usages ? Comment les acteurs académiques forment-ils leurs étudiants à cette technologie sans cesse évolutive ? Et comment ensemble ils cherchent à répondre aux nouveaux défis de l'impression 3D (écoconception, design génératif, valorisation des déchets…) ?
Deux experts apporteront leurs regards sur ce sujet :
► Christine BILLON-LANFRAY, Responsable Plateforme Technologique Académique & Smartech Pôle S.mart RAO (INSA Lyon)
► Florian BERTHELOT, Co-fondateur F3DF Une table ronde ouverte à toutes et tous, organisée par la Fabrique de l'Innovation, en partenariat avec "Les Soudés", collectif d'experts du prototypage industriel
Inscription en ligne => Regards croisés #1 - Fabrication additive, fabrication addictive
Additional informations
- fabrique.innovation@universite-lyon.fr
- https://fabriqueinnovation.universite-lyon.fr/regards-croises-1-fabrication-additive-fabrication-addictive--285331.kjsp?RH=16082
-
Pré-Fabrique de l'Innovation - 28-30 avenue Gaston Berger 69100 Villeurbanne
Keywords (tags)
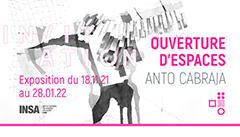
Art & Culture
Exposition "Ouverture d'espaces" d'Anto Cabraja
Artiste résident à l’INSA d’octobre 2021 à janvier 2022, Anto Cabraja explore les formes d’impression, les différents supports et dimensions (papier, 2D, 3D, sculpture, numérique).
Fluidité des frontières entre le crayon, la plume, le pinceau et le style
Dans le cadre de sa politique de soutien aux artistes, le macLYON a accueilli durant quatre mois (début 2021) Anto Cabraja pour lui permettre de travailler sur le projet qu’il nous présente aujourd’hui.
Dans l'espace de la création, l'artiste tout comme le scientifique, rencontrent tous deux la matière et l'esprit à un moment donné de leur processus de conception et réalisation. Tandis que l'un accède au sensoriel directement, l'autre le fait à travers une représentation mentale qui peut avoir une relation directe avec l'image sur la rétine.
L’un comme l'autre vont rencontrer la beauté́ de la forme sans passer par une représentation intermédiaire.
Gratuit et ouvert à tous sur inscription => https://bit.ly/expo-ouverture-despaces
Additional informations
-
Galerie du centre des Humanités - 1 rue des Humanités 69100 Villeurbanne - Tramway T1/T4 - Station INSA-Einstein ou La Doua-Gaston Berger
Keywords (tags)
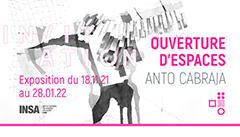
Art & Culture
Vernissage exposition "Ouverture d'espaces" d'Anto Cabraja
Artiste résident à l’INSA d’octobre 2021 à janvier 2022, Anto Cabraja explore les formes d’impression, les différents supports et dimensions (papier, 2D, 3D, sculpture, numérique).
Fluidité des frontières entre le crayon, la plume, le pinceau et le style
Dans le cadre de sa politique de soutien aux artistes, le macLYON a accueilli durant quatre mois (début 2021) Anto Cabraja pour lui permettre de travailler sur le projet qu’il nous présente aujourd’hui.
Dans l'espace de la création, l'artiste tout comme le scientifique, rencontrent tous deux la matière et l'esprit à un moment donné de leur processus de conception et réalisation. Tandis que l'un accède au sensoriel directement, l'autre le fait à travers une représentation mentale qui peut avoir une relation directe avec l'image sur la rétine.
L’un comme l'autre vont rencontrer la beauté́ de la forme sans passer par une représentation intermédiaire.
Additional informations
-
Galerie du centre des Humanités - 1 rue des Humanités 69100 Villeurbanne - Tramway T1/T4 - Station INSA-Einstein ou La Doua-Gaston Berger
Keywords (tags)
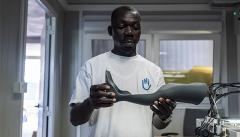
Recherche
Innovation for Humanity : innover pour réparer l’humain
« À l’heure actuelle, des millions de personnes à travers le monde ont besoin d’une prothèse mais n’y ont pas accès en raison du coût matériel, du manque de ressources humaines expertes et de la difficulté à se déplacer dans un centre de santé. » Tel est le constat énoncé par Pierre Gallien, directeur innovation, impact & information d’Handicap International.
La réadaptation physique et fonctionnelle est le premier sujet de recherche qui amorcera les collaborations scientifiques menées dans le cadre d’une alliance unissant le Groupe INSA et la Fédération Handicap International. Dans le cadre de la chaire de recherche et d’enseignement « Innovation for Humanity » lancée le 28 janvier prochain, les chercheurs de l’INSA auront pour objectif de répondre aux problématiques rencontrées par les équipes de l’organisation humanitaire. Abder Banoune et Jérôme Chevalier, tous deux impliqués dans cette chaire, expliquent comment la recherche peut participer à restaurer l’intégrité physique des personnes handicapées, avec une contrainte : celle de faire « avec ce qu’il y a sur place ».
Dans le monde et selon l’Organisation Mondiale de la Santé, seulement 5% à 15% des personnes ayant besoin de technologie d’assistance (fauteuils, prothèses et orthèses, aides à la mobilité aides auditives et visuelles) y ont accès. Accompagner les personnes handicapées vers l’autonomie est le métier originel d’Handicap International, et malgré plus de 40 ans d’action, les défis humanitaires restent nombreux. Abder Banoune, spécialiste de la réadaptation physique au sein de l’ONG, explique. « L’une de nos missions fondamentales est d’accompagner des personnes victimes à récupérer une mobilité optimale. Nous intervenons principalement dans des pays frappés par des conflits, des catastrophes naturelles ou une extrême pauvreté et où l’accès à des prothèses ou des orthèses est rendu difficile. Aujourd’hui, pour rendre une prothèse disponible, nous avons besoin d’équipements lourds et d’équipes très qualifiées, ce qui est souvent incompatible avec les situations des pays dans lesquels nous intervenons. »
Les promesses de l’impression 3D
Après des analyses de terrain, les équipes d’Handicap International ont réalisé le potentiel de l’impression 3D. Des projets pilotes ont démontré que cette technologie pouvait notamment répondre à une problématique logistique de taille. « Lorsqu’un patient a besoin d’un appareillage orthopédique, il doit se rendre dans un centre médical situé dans les grandes villes. S’il vit dans une zone rurale ou de montagne, l’accès au centre peut s’avérer compromis. L’impression 3D nous permet de nous rapprocher au plus près des personnes dans le besoin : avec un simple ordinateur et un scanner nous pouvons prendre les mesures physiologiques des patients et envoyer les données à un centre de fabrication dans les grandes villes. Mais pour ouvrir cette technologie à plus de personnes, nous avons ici besoin de la recherche », poursuit Abder.
Identifier des axes de recherche scientifique pour soigner plus de patients
Au cours des derniers mois, les laboratoires et les équipes les plus pertinentes sur le sujet de l’impression 3D de prothèses et orthèses ont été sollicités. Parmi les laboratoires identifiés, l’IMP1, spécialiste des polymères ; le laboratoire MATEIS2, expert dans le domaine des propriétés mécaniques et de la durabilité des matériaux ; et le LaMCoS3, pour son expertise sur la conception et la fabrication additive. « Avec Christophe Garcia, également porteur de la chaire, nous avons pour mission de traduire la feuille de route transmise par Handicap International en projets de recherche. Après avoir identifié les besoins, nous allons transformer chaque sujet en projets de fin d’études et en thèses de doctorat. Il est essentiel d’impliquer les étudiants, d’une part car ils sont très demandeurs de ces sujets porteurs de sens et d’autre part parce qu’ils ont aussi de belles idées qui méritent d’être développées », dit Jérôme Chevalier, enseignant-chercheur adjoint à la direction de la recherche de l’INSA Lyon et porteur de la chaire.
De l’optimisation de la prothèse imprimée…
Pour les chercheurs, la question est donc posée : comment optimiser l’impression 3D de prothèses et d’orthèses, pour soigner plus de patients dans le besoin ? De l’élaboration à la résistance des matériaux, en passant par la durabilité des composants ou l’optimisation des formes et des architectures, les challenges scientifiques sont nombreux. « D’abord, nous souhaiterions travailler à l’optimisation des prothèses en elles-mêmes. Aujourd’hui, elles sont fabriquées par thermoformage et avec des matériaux qui ne sont pas toujours disponibles dans les pays d’intervention d’Handicap International. La fabrication additive par impression 3D permet d’étudier de nouvelles possibilités de formes et d’évaluer l’utilisation de matières premières accessibles localement », explique Jérôme Chevalier également chercheur au laboratoire MATEIS.
… à une imagerie médicale adaptée.
Dans un second temps, c’est la question de l’imagerie qui sera traitée par les équipes de chercheurs. « Pour fabriquer une prothèse de façon classique, il faut reproduire la partie du corps faisant défaut avec un moule de plâtre. Aujourd’hui, dans les pays d’intervention, ce matériau une fois utilisé, est directement jeté. Le recyclage des déchets induits par la fabrication de prothèses et d’orthèses est un vrai sujet. L’impression 3D limiterait la production de déchets, voire permettrait de réutiliser certains déchets plastiques. Nous pourrions aussi imaginer prendre les mesures physiologiques sur place, directement avec l’appareil photo d’un téléphone portable au lieu d’un scanner. À partir de cela, il n’y aurait plus besoin de plâtre. Pour arriver à cela, nos équipes devront travailler à la traduction de l’empreinte 3D en modèle pour les imprimantes », poursuit l’enseignant-chercheur.
Quatre années pour la recherche au service de causes humanitaires
Alors que le premier volet de la chaire de recherche unissant l’INSA et Handicap International commence à prendre corps, « Innovation for Humanity » ne s’arrêtera pas en si bon chemin. Signée pour 4 ans minimum, la collaboration donnera lieu à des recherches sur l’utilisation de drones pour déminage, l’analyse d’images et de données et plus généralement l’apport des sciences numériques, avec pour même objectif de faire émerger des enjeux scientifiques aux problématiques rencontrées sur le terrain par les équipes de l’organisation internationale. « Le monde évolue, il doit en aller de même pour nos formations et notre recherche. L’humanitaire doit également profiter de nos recherches », conclut Jérôme Chevalier.
1 Laboratoire Ingénierie des Matériaux Polymères (CNRS / UdL / Lyon1 / UJM / INSA Lyon)
2 Matériaux : ingénierie et sciences (INSA Lyon/ CNRS / Lyon 1)
3 Laboratoire de Mécanique des Contacts et des Structures (INSA Lyon / CNRS / UdL)
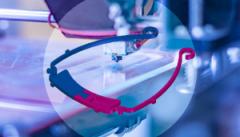
Recherche
Oyonnax : l’INSA Lyon entre dans la grande famille des « makers »
Le pari des « makers » est de fabriquer des masques de protection de substitution destinés aux personnels soignants, à partir des outils de fabrication additive à leur disposition. Les plans de conception sont en libre accès et les matières premières partagées entre tous les makers. Sur le Campus d’Oyonnax, Hayet Lakhdar a rejoint le réseau et fait tourner chaque jour, les imprimantes 3D de la plateforme dont elle est responsable. Grâce à sa présence sur le site de production, personnels soignants, agents de sûreté et travailleurs en première ligne peuvent bénéficier d’une protection supplémentaire aux masques de protection classiques, dont ils manquent encore. Explications.
La démarche est nationale. Pour faire face à la rupture d’approvisionnement en masques de protection, bricoleurs, propriétaires particuliers ou professionnels d’imprimantes 3D se sont organisés pour produire et fournir, non pas des masques mais des visières de protection en plastique aux travailleurs en première ligne dans la lutte contre le Covid-19. Hayet Lakhdar est ingénieure d’études et responsable de la plateforme Labo du campus INSA d’Oyonnax. En pleine Plastics Vallée, il était naturel de rallier la cause de ces confectionneurs de solutions alternatives en plastique, le réseau des « makers » qui met en relation fabricants et professionnels de santé. Hayet revient sur le début des opérations. « Après avoir fait don de nos masques et blouses que nous avions recensés dans les différents laboratoires et stocks sur le campus, nous avons voulu aller plus loin et mettre nos expertises en impression 3D à disposition des personnes qui en ont besoin aujourd’hui. Sur les réseaux sociaux, je suis tombée sur un fichier technique de fabrication de masques de substitution. La solution était plutôt simple : une visière de protection composée d’un serre-tête imprimé en 3D augmenté d’une feuille de plastique transparent pour barrière, et d’un élastique à nouer derrière la tête », explique Hayet.
Rapidement, elle créé ses propres programmes pour lancer les machines de la plateforme. « Les premières visières ont été faites de feuilles transparentes en PVC d’un vieux stock qui traînait dans nos archives ! On fixe la feuille en plastique sur un serre-tête imprimé sur nos machines et le tour est joué. Entre l’INSA et l’IPC (Centre technique Industriel de la Plasturgie et des Composites), une cinquantaine de masques par jour sont créés. Aujourd’hui, nous avons allié nos forces avec nos industriels voisins, le lycée Arbez Carme et le pôle de compétitivité Plastipolis. Nous voulons aller plus loin dans la production de masques plus techniques et performants », poursuit Hayet Lakhdar.
Depuis deux semaines, l’ingénieure d’études se rend quotidiennement sur la plateforme de production du campus oyonnaxien. Les premiers jours, Hayet distribuait ses productions aux personnes de son entourage, directement impliquées dans le combat, pour se protéger des potentiels porteurs du Covid-19. « J’ai transmis les premières visières à des infirmières de ma connaissance. Cela leur sert de double protection : la visière vient en barrière des postillons et gouttelettes dans lesquels la souche du Coronavirus se loge et se transmet. Les demandes pour ce type de protection ont été exponentielles. Il a fallu nous organiser localement pour la distribution qui est désormais centralisée depuis une pharmacie de la région qui s’occupe de redistribuer aux professionnels de santé », dit Hayet. Seule sur le site de production de la plateforme Labo, mesures de confinement obligent, l’ingénieure d’étude a les idées larges. Pour les semaines à venir, elle souhaite augmenter le nombre de masques produits tout en les rendant plus techniquement avancés. « Avec les sociétés Dalloz Créations et SMP, nous travaillons au développement d’une visière injectée de gamme supérieure, plus rapide à produire que celle issues de machines de fabrication additive », conclut Hayet Lakhdar.
Partout en France, des imprimantes 3D dessinent de leurs fils plastiques fondus, des visières de protection, des pousse-seringues ou même des poignées de portes sans contact. Qu’ils soient des particuliers, des industriels ou des personnes organisés en fablabs, les adeptes de la fabrication additive semblent avoir donné naissance à « une économie de la débrouille » inspirée de nouvelles formes d’entraide et de coopération. Bien plus que le modeste concept du « Do It Yourself » avec des espaces numériques partagés et une mise à disposition libre des connaissances, les makers comme Hayet Lakhdar annonceraient-ils les prémices d’une productivité régénérée, loin des principes productivistes de l’ère de l’avant-confinement ?
Sur le campus lyonnais, enseignants et étudiants se sont également lancés dans la production de masques, visières, valves et ouvre-portes pour les personnels soignants. « Lorsque j’ai entendu parler de l’initiative, j’ai contacté les professeurs de l’INSA Lyon responsables de l’opération. J’ai proposé mon aide dans la recherche de fournisseur de matières premières comme les feuilles transparentes qui servent d’écran ou les bobines d’impression 3D dont nous avons besoin. C’est ma façon d’apporter ma pierre à l’édifice dans ce soutien aux personnels soignants », explique Lina Borg, étudiante en 1re année de FIMI à l’INSA Lyon. Certains laboratoires disposant de machines de fabrication additive comme le LMFA, le LaMCos et le CETHIL ont aussi rejoint le mouvement.
Le projet collaboratif, nommé Lyon education anti covid-makers est basé sur le bénévolat, les dons en matières premières et en dons financiers.
Pour aller plus loin, ils ont recensé les besoins suivants :
· plaques de plastique d'épaisseur 5 ou 6mm pour découpe laser : PE, PETG, POM C, PA6, PA6.6 ou PMMA notamment,
· feuilles de plastique transparent pour les écrans des visières,
· filament ABS, PLA, PETG diamètre 1,75mm ou 3mm,
· plastiques pour maintien de visières ou de masques.
Si vous êtes en possession d’une imprimante 3D ou une machine découpe laser, l’équipe recherche des volontaires.
Pour soutenir le projet : je fais un don
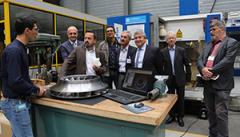
Recherche
AIP Primeca RAO : en route vers l’industrie du futur
La plateforme technologique académique AIP-Primeca RAO fête ses 30 ans d’existence et continue d’investir, grâce au soutien de ses établissements partenaires et du Conseil Régional. Déjà clairement visible sur les champs de la mécatronique, de la fabrication additive ou encore des systèmes automatisés de production, elle développe des process d’accompagnement aux start-ups mais aussi à la formation pour l’industrie du futur. Ambition.
« On peut travailler tout seul, mais en réseau c’est plus efficace ». Voilà en quelques mots la ligne de conduite de Didier Noterman, Directeur de l’AIP-Primeca Rhône-Alpes Ouest basé sur le campus de l’INSA Lyon.
Depuis 12 ans, il dirige ce pôle unique dans le paysage de l’enseignement supérieur, créé pour mutualiser des ressources, fédérer des compétences et développer l’ingénierie pédagogique associée dans les domaines de la productique, de la mécatronique, de l’impression 3D, de la métrologie et des ressources informatiques pour la mécanique.
Son challenge actuel est celui de beaucoup d’industries : réussir la transition numérique.
« Aujourd’hui, nous continuons à investir dans les champs d’activités du pôle, qui correspondent à ceux de l’industrie du futur. Nous essayons de sélectionner nos fournisseurs de manière à ce qu’ils deviennent nos partenaires pour construire ensemble cette industrie 4.0 » explique Didier Noterman.
En 4 ans, les effectifs du pôle AIP-Primeca ont doublé et grâce à ses nouveaux projets, les coups de fil pleuvent. A l’ordre du jour, la création d’une plateforme usine connectée en lien avec 4 partenaires industriels historiques pour établir ce que seront les normes de l’industrie du futur. Les sociétés Schneider-Electric, Staübil robotics, Actemium, PTC et Wonderware sont parties prenantes de cette réflexion qui a obtenu le soutien financier de la région Auvergne Rhône-Alpes.
Autre projet de développement : la formation, et plus précisément la réorientation des étudiants « en échec » à l’université vers les métiers en tension au niveau régional.
« C’est parti d’un constat simple : il y a beaucoup d’étudiants qui décrochent en licence à l’université et qui pourraient être détectés pour être réorientés et développer des compétences dont les entreprises ont un besoin criant. Nous voudrions détecter ces talents cachés, les mettre à niveau sur 10 semaines de formations au pôle AIP avec nos partenaires AFPA, INSAVALOR et leur permettre ensuite, soit de continuer sur une formation adaptée plus longue, soit d’être directement embauchés » précise Didier Noterman.
Ce principe soutenu par la Région conduirait à la mise en place des formations dès 2018, avec 3 sessions de 20 places par an sur les domaines de l’automatisme et de la robotique ; de l’électronique et des objets connectés ; du graphisme et du design et enfin de la mécanique et l’impression 3D.
Un hôtel à projets pour entrepreneurs innovants
C’est l’actualité qui stimule les énergies du pôle AIP-Primeca. Financé par l’aide de la région Auvergne Rhône-Alpes, cet hôtel à projets a pour objectif d’accueillir des entrepreneurs innovants en résidence et de leur offrir une assistance technologique. 4 ou 5 start-ups pourraient rejoindre le centre d’innovation technique AIP-Primeca dans de futurs locaux mis à disposition sur le campus de l’INSA Lyon. Une première start-up, PaintUp, est actuellement en résidence sur le campus avec le projet de développer un système robotisé autonome destiné au nettoyage et la peinture de façades ou de surfaces de grande dimension.
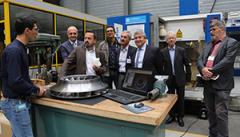
Recherche
AIP Primeca RAO : en route vers l’industrie du futur
La plateforme technologique académique AIP-Primeca RAO fête ses 30 ans d’existence et continue d’investir, grâce au soutien de ses établissements partenaires et du Conseil Régional. Déjà clairement visible sur les champs de la mécatronique, de la fabrication additive ou encore des systèmes automatisés de production, elle développe des process d’accompagnement aux start-ups mais aussi à la formation pour l’industrie du futur. Ambition.
« On peut travailler tout seul, mais en réseau c’est plus efficace ». Voilà en quelques mots la ligne de conduite de Didier Noterman, Directeur de l’AIP-Primeca Rhône-Alpes Ouest basé sur le campus de l’INSA Lyon.
Depuis 12 ans, il dirige ce pôle unique dans le paysage de l’enseignement supérieur, créé pour mutualiser des ressources, fédérer des compétences et développer l’ingénierie pédagogique associée dans les domaines de la productique, de la mécatronique, de l’impression 3D, de la métrologie et des ressources informatiques pour la mécanique.
Son challenge actuel est celui de beaucoup d’industries : réussir la transition numérique.
« Aujourd’hui, nous continuons à investir dans les champs d’activités du pôle, qui correspondent à ceux de l’industrie du futur. Nous essayons de sélectionner nos fournisseurs de manière à ce qu’ils deviennent nos partenaires pour construire ensemble cette industrie 4.0 » explique Didier Noterman.
En 4 ans, les effectifs du pôle AIP-Primeca ont doublé et grâce à ses nouveaux projets, les coups de fil pleuvent. A l’ordre du jour, la création d’une plateforme usine connectée en lien avec 4 partenaires industriels historiques pour établir ce que seront les normes de l’industrie du futur. Les sociétés Schneider-Electric, Staübil robotics, Actemium, PTC et Wonderware sont parties prenantes de cette réflexion qui a obtenu le soutien financier de la région Auvergne Rhône-Alpes.
Autre projet de développement : la formation, et plus précisément la réorientation des étudiants « en échec » à l’université vers les métiers en tension au niveau régional.
« C’est parti d’un constat simple : il y a beaucoup d’étudiants qui décrochent en licence à l’université et qui pourraient être détectés pour être réorientés et développer des compétences dont les entreprises ont un besoin criant. Nous voudrions détecter ces talents cachés, les mettre à niveau sur 10 semaines de formations au pôle AIP avec nos partenaires AFPA, INSAVALOR et leur permettre ensuite, soit de continuer sur une formation adaptée plus longue, soit d’être directement embauchés » précise Didier Noterman.
Ce principe soutenu par la Région conduirait à la mise en place des formations dès 2018, avec 3 sessions de 20 places par an sur les domaines de l’automatisme et de la robotique ; de l’électronique et des objets connectés ; du graphisme et du design et enfin de la mécanique et l’impression 3D.
Un hôtel à projets pour entrepreneurs innovants
C’est l’actualité qui stimule les énergies du pôle AIP-Primeca. Financé par l’aide de la région Auvergne Rhône-Alpes, cet hôtel à projets a pour objectif d’accueillir des entrepreneurs innovants en résidence et de leur offrir une assistance technologique. 4 ou 5 start-ups pourraient rejoindre le centre d’innovation technique AIP-Primeca dans de futurs locaux mis à disposition sur le campus de l’INSA Lyon. Une première start-up, PaintUp, est actuellement en résidence sur le campus avec le projet de développer un système robotisé autonome destiné au nettoyage et la peinture de façades ou de surfaces de grande dimension.