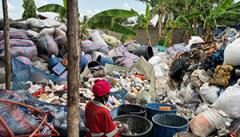
Investigación
Transformer les plastiques recyclés en appareillages orthopédiques pour les populations vulnérables
D’après l’OMS, seulement 5 à 15 % des personnes ayant besoin d’un appareil orthopédique y ont accès dans les pays à faibles revenus ou en contexte de guerre. Pour pallier ce constat, Handicap International a intégré l’impression 3D sur ses territoires d’intervention depuis 2017. Aujourd’hui, l’organisation non gouvernementale se voit confrontée à des problématiques logistiques coûteuses, liées à l’importation de la matière première depuis l’Europe. Et s’il était désormais possible de fabriquer des appareillages orthopédiques à base de plastiques recyclés, trouvés localement ?
Orthèse fabriquée par impression 3D au Togo.
(Handicap International, Author provided).
Au sein de l’INSA Lyon, Valentine Delbruel, ingénieure INSA et doctorante, travaille sur l’optimisation de la composition d’un plastique recyclé, qui pourrait convenir à la fabrication additive d’orthèses : une façon de lutter contre la pollution plastique tout en rendant plus accessibles les solutions orthopédiques. Réalisés en collaboration avec Handicap International et trois laboratoires de l’INSA Lyon (MatéIS, IMP et LaMCoS), les travaux de la doctorante serviront aux équipes terrain d’Handicap International.
L’impression 3D : une innovation pratique mais une logistique difficile
Traditionnellement réalisés par thermoformage, les appareillages orthopédiques relèvent d’un procédé de fabrication long et coûteux. Dans les zones où l’accès aux centres de soin est déjà difficile, les aller-retours nécessaires aux ajustements et le temps de rééducation sont des freins supplémentaires, rallongeant la procédure de soin de plusieurs semaines pour une prothèse. Depuis 2017, Handicap International utilise l’impression 3D pour pallier ce problème. Les fabrications sont facilitées, plus rapides et personnalisables à chaque patient. « L’impression 3D a changé la façon de prendre les mensurations des patients car elles peuvent être prises à distance grâce à un scanner 3D », explique Valentine Delbruel. « Seulement, ce type de fabrication nécessite des filaments composés de plastique qui sont actuellement fabriqués en Europe. Cela pose des problèmes logistiques, notamment aux niveaux des frontières. En constatant cette problématique rencontrée par ses équipes, Handicap International s’est interrogé : est-il possible de continuer à faire de l’impression 3D, avec des matières plastiques locales, si possible recyclées ? »
Le procédé de fabrication des orthèses par thermoformage classique est long et coûteux.
(©Valentine Delbruel)
Utiliser du plastique recyclé pour soigner et dépolluer grâce à l’impression 3D : un projet vertueux, mais ambivalent, comme l’a constatée Valentine lors d’un voyage d’observation au Togo. « Dans de nombreux pays d’Afrique, le service de collecte des déchets est un service payant. Souvent un luxe pour les familles à faibles revenus, ce manque de service public engendre une pollution plastique importante dans les milieux naturels. Faire du déchet plastique une ressource pour les foyers tout en répondant à un besoin d’accès à la santé serait doublement bénéfique. »
Des enjeux de durabilité et de solidité du matériau recyclé
Sur le papier l’idée tombe sous le sens, mais les enjeux scientifiques et techniques soulevés par la potentielle réutilisation de plastiques recyclés ne sont pas si simples à solutionner. « Les deux principales problématiques sont celles de l’imprimabilité de la matière recyclée et de sa durabilité ». D’une part, les propriétés rhéologiques1 des matériaux sont étudiées. « Il faut une viscosité suffisamment faible pour que la matière s’écoule lors de l’impression, et dans le même temps, s’assurer que celle-ci maintienne sa forme une fois déposée ». D’autre part, il faut que la matière finale soit assez résistante pour durer dans le temps. « Et ça n’est pas une chose facile lorsque l’on mélange différents polymères », indique la doctorante qui réalise depuis trois années, différentes expérimentations afin de trouver la meilleure recette. « Il a fallu caractériser les déchets dans les pays d’intervention, qui ne sont pas nécessairement les mêmes que chez nous. Par exemple, j’ai d’abord testé les emballages alimentaires, avant de m’apercevoir lors de ma mission au Togo qu’il y en avait très peu ! Il faut principalement composer avec des bouteilles en Polyéthylène Téréphtalate (PET) et des produits du quotidien en Polypropylène (PP) et polyéthylène (PE). »
Les déchets plastiques pourraient être une ressources pour les foyers.
(©Valentine Delbruel)
Mettre les compétences des laboratoires à l’épreuve du terrain
Si Valentine Delbruel sait pouvoir compter sur les expertises scientifiques de trois laboratoires (le laboratoire MatéIS sur la structure et la propriété des matériaux, le laboratoire IMP expert dans l’élaboration et la caractérisation des matériaux polymères et le laboratoire LamCoS, spécialisé dans la mécanique des contacts et des structures), il n’en reste pas moins une tâche importante pour la doctorante en sciences appliquées : s’assurer de rester au plus proche du terrain pour produire une solution utile à destination des équipes d’Handicap International et des patients. « On a testé la résistance de nos matériaux recyclés dans les conditions climatiques africaines (température, humidité et exposition UV) grâce à une chambre climatique de vieillissement accéléré présente à l’INSA Strasbourg2. Dans le même temps, nous avons conçu un banc d’essai3 qui reproduit le mouvement de la marche et nous permettra d’étudier la résistance en fatigue des orthèses en sollicitations cycliques. Nous pouvons faire nos essais sur des orthèses imprimées en échelle 1 avec les mêmes imprimantes 3D utilisées par l’ONG, ce qui nous permet d’être le plus représentatif des conditions réelles. »
Tests en laboratoire par impression 3D
(©Valentine Delbruel)
Pour l’heure, l’ingénieure est formelle : « Il est encore difficile d’utiliser les matières issues d’usine de recyclage à cause de la présence d’impuretés. Si l’imprimabilité des matières recyclées en France est possible, la qualité des gisements d’Afrique n’est pas encore suffisante. C’est pourquoi pour ma dernière année de thèse, je m’intéresse plutôt au recyclage des chutes de plaques orthopédiques générées lors du thermoformage de prothèses ou orthèses. Il s’agit de matériaux de grande qualité qui sont actuellement jetés. En les recyclant, nous limitons l’utilisation de matières vierges et donc de ressources naturelles. Il sera alors intéressant d’étudier jusqu’à combien de cycles de recyclage la matière conserve ses propriétés mécaniques, afin d’avoir la solution la plus circulaire possible », conclut Valentine Delbruel.
La doctorante soutiendra ses travaux à la fin septembre 2024, date à laquelle elle espère pouvoir apporter le plus d’éléments possibles à l’ONG pour offrir une solution aux équipes de terrain et aux patients des zones à faibles revenus ou de guerre.
Plus d’informations : https://www.groupe-insa.fr/nos-actualites/chaire-innovation-humanity-entretiens-croises
[1] La rhéologie est un domaine de la mécanique qui étudie la résistance des matériaux aux contraintes et aux déformations.
[2] Collaboration réalisée avec Vincent Steiner de l’INSA Strasbourg
[3] Les travaux de thèse de Valentine Delbruel ont été accompagnés par deux projets de fin d’études d’élèves-ingénieurs du département Matériaux et Génie Mécanique : l’un sur la résistance en conditions climatiques d’Afrique (Hugo Lajoie) ; l’autre sur la fabrication d’un banc d’essai reproduisant le mouvement de la marche (Abderrahmane Abbassi).